炭酸飲料は、飲み物に二酸化炭素ガスを加えることで作られた飲み物です. 彼らはユニークな陽気な味とさわやかな味を持っています. さまざまな種類があります, コーラを含む, スプライト, そしてフルーツ風味のソーダ, 世界中の消費者に愛されています. 炭酸飲料は、味に刺激と喜びをもたらすだけではありません, しかし、多くの場合、果物の味と組み合わされます, ハーブ成分, または、さまざまなグループの人々のニーズを満たすための機能的な式.
容量: 2000-42000 bottles/hour
Filling Accuracy: ≤±5mm (液体レベルのポジショニング)
該当するボトルタイプ: Round or Square
Applicable Cap Type: Plastic Screw Cap
Bottle Rinsing Water Pressure (MPA):0.2~0.25
PET Bottle Specifications: ボトル径out50~100, Bottle Height 150mm~330mm
Applicable beverage types: water, tea drinks, ジュース, functional drinks, water, ソーダ, 等.
Tel: +86 371-86582811
Mob & Whatsapp: +86 15239453015
メール: info@hadofmachinery.com
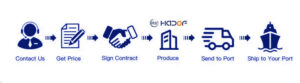
Parameter
Technical Parameters | HDF8-8-4 | HDF14-12-5 | HDF16-16-5 | HDF20-20-6 | HDF24-24-8 | HDF32-32-10 | HDF40-40-12 | HDF50-50-15 |
Production Capacity (500ml/B/H) | 2000-3000 | 3000-4000 | 4000-5000 | 5000-7000 | 8000-10000 | 10000-12000 | 14000-15000 | 16000-18000 |
Specifications | 60π | 50π | 50π | 50π | 45π | 45π | 40π | 36π |
Bottle Rinse Usage (Kg/h) | 500 | 600 | 700 | 800 | 1500 | 1800 | 2500 | 3000 |
Air Source Pressure (MPA) | 0.4 | 0.4 | 0.4 | 0.4 | 0.4 | 0.4 | 0.4 | 0.4 |
Air Consumption (m³/min) | 0.3 | 0.3 | 0.3 | 0.3 | 0.4 | 0.4 | 0.5 | 0.55 |
Total Power (Kw) | 2.5 | 3 | 3.3 | 3.8 | 4.2 | 5.6 | 6.4 | 9.8 |
Dimensions (L×W×H) (mm) | 1950×1450×2350 | 2260×1600×2350 | 2350×1900×2350 | 2900×2200×2400 | 3300×2300×2400 | 4100×2850×2400 | 4250×3200×2400 | 5750×3750×2400 |
Total Weight (Kg) | 2500 | 2800 | 3000 | 4000 | 5000 | 6500 | 8000 | 9000 |
Water Treatment
Blow Molding
Mixing
Filling
Cooling
Labeling
Packaging
Palletizing
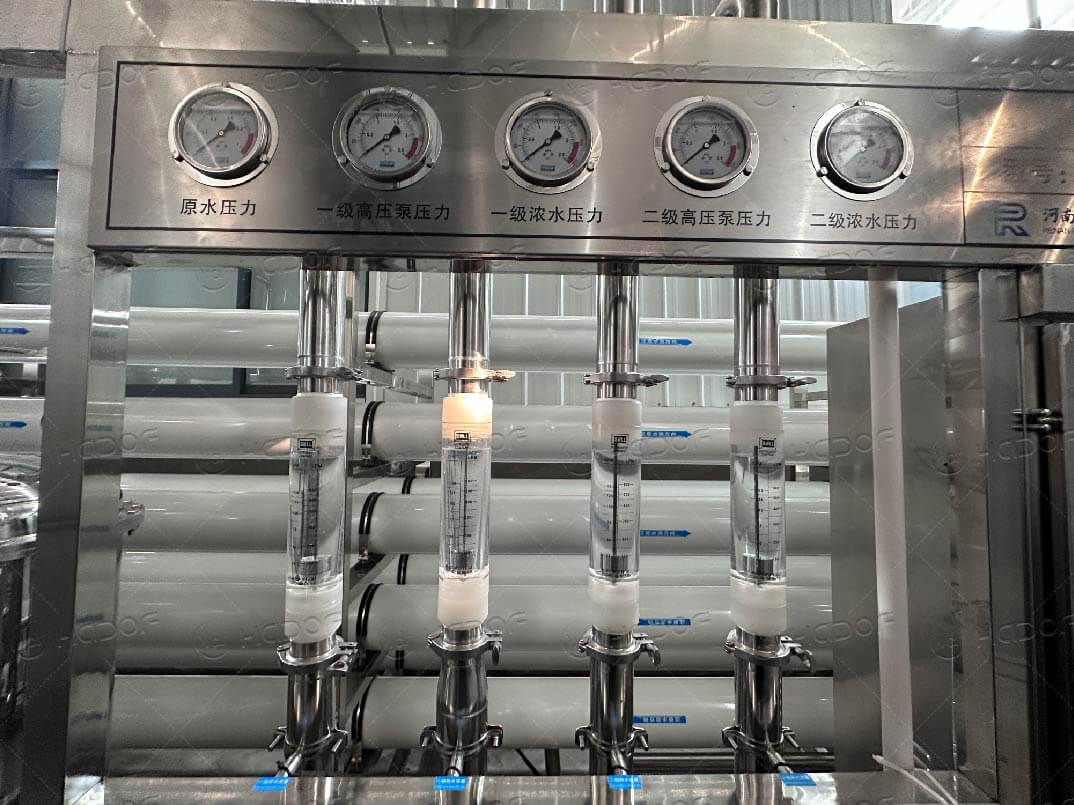
1. Water Treatment System:
Water treatment is a critical step to ensure the quality of the soda water. The production line uses advanced reverse osmosis equipment for deep purification.
Multiple steps including sedimentation, 濾過, and disinfection ensure water quality.
– Organic matter, metal oxides, suspended solids, bacteria, and colloids are removed from the water.
– After treatment, the water meets the required purity standards for soda water production.
– The purified water is now ready for use in the mixing process.
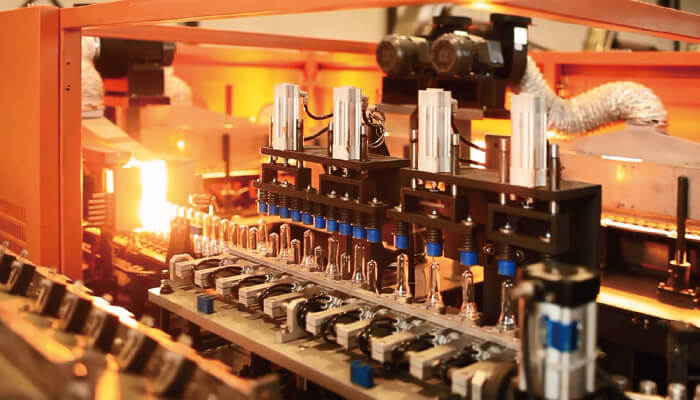
2. Blowing Equipment:
– The preforms enter the blow molding machine through the conveying system.
– The preforms are preheated in the oven and heated evenly.
– The preforms are formed and output under the action of high-pressure gas.
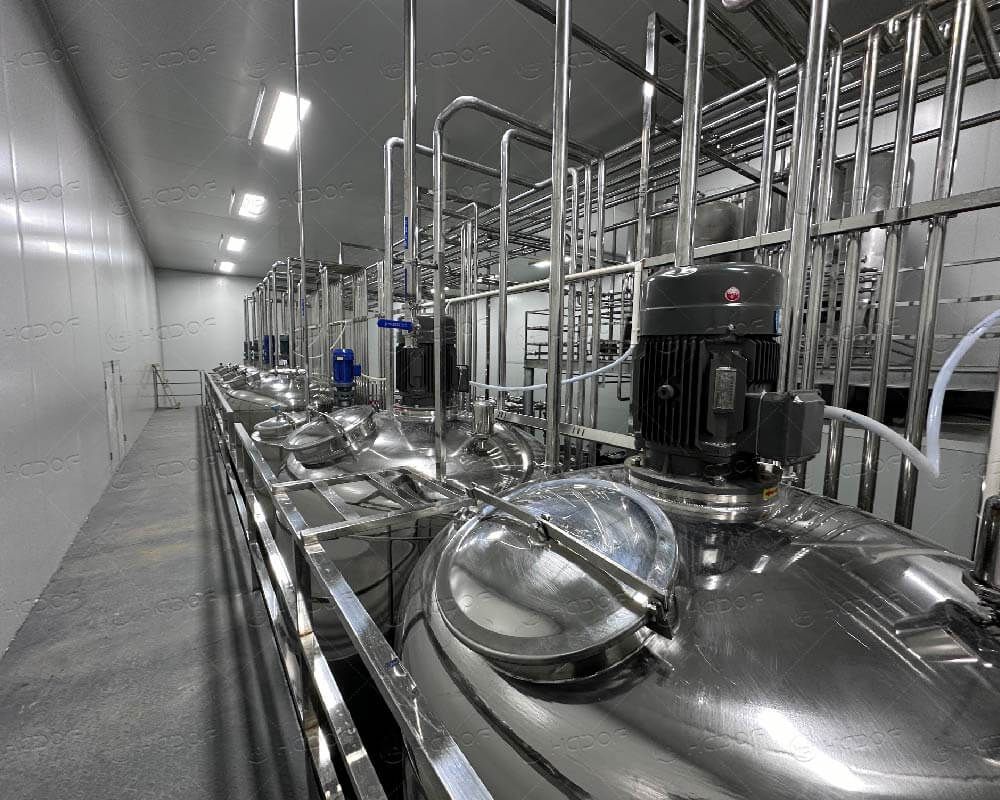
3. Blending, Cooling And Mixing Systems:
– Mixing of water, syrup and CO2.
– Sugar dissolving pot and blending tank for making syrup.
– Beverage mixer for filtering and mixing.
– Vacuum degassing and proportioning system for optimized mixing.
– CO2 jet technology for improved taste.
– Plate heat exchanger for cooling to 0℃~3℃.
– Carbonation is done in CO2 mixing tank.
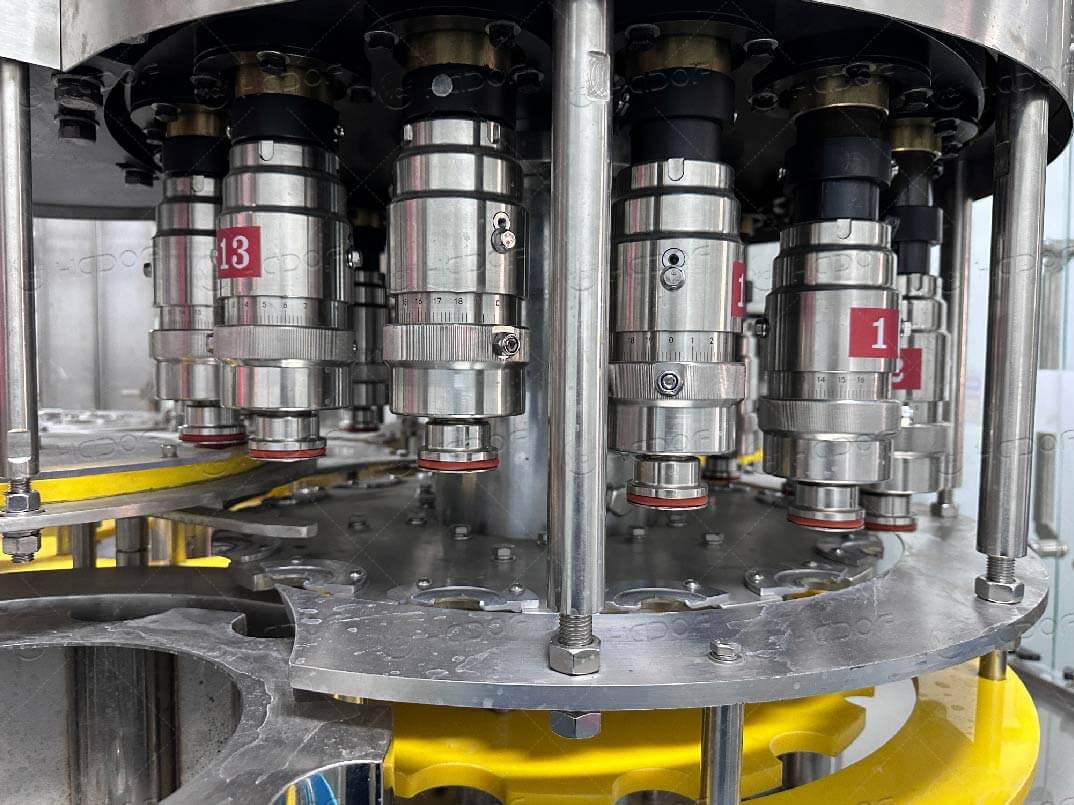
4.Filling system:
– The material enters the filling machine cylinder and the flow is controlled by a pneumatic diaphragm valve.
– Plastic bottles: air conveying device and hanging bottleneck method are used for bottle washing, isobaric filling and capping.
– Glass bottles: air conveying and water spray cleaning, isobaric filling, electromagnetic capping.
– Cans: After normal pressure filling, the capping system completes pre-sealing and actual sealing.
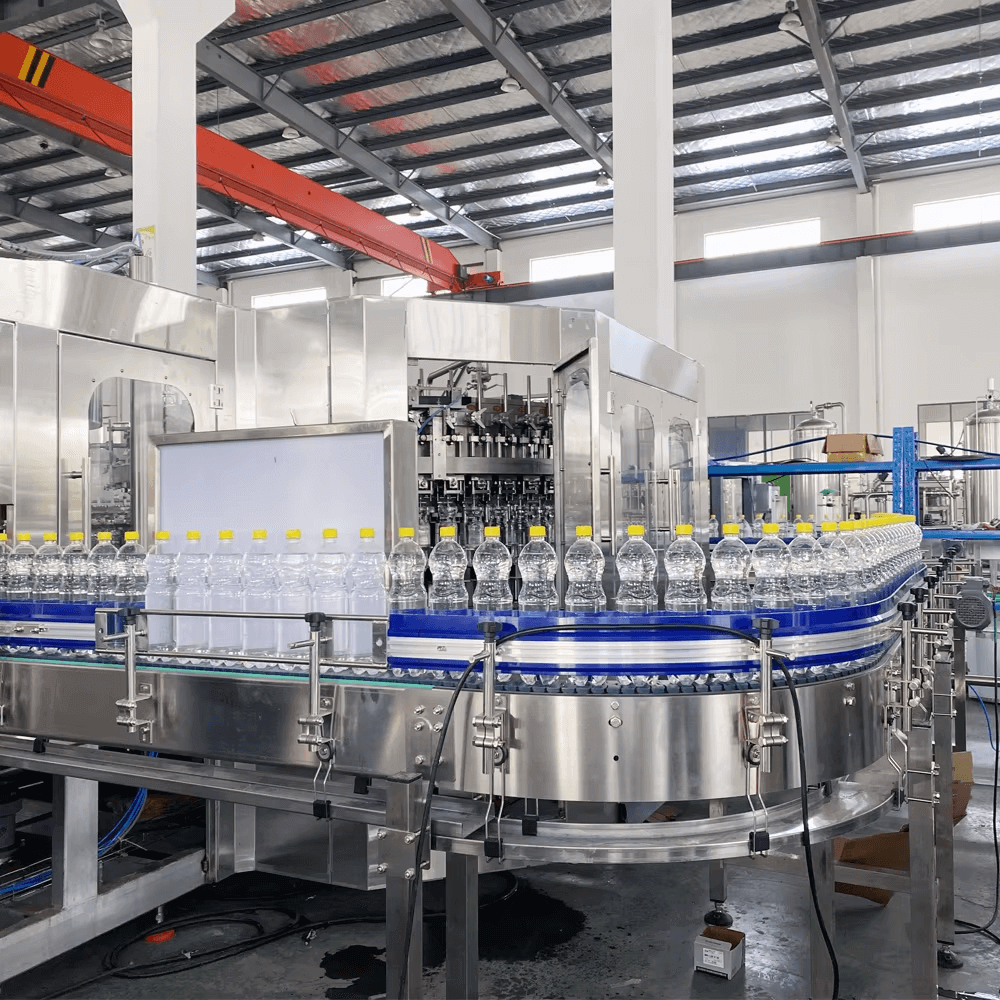
5. Spray cooling system
The spray cooling system sprays a cooling liquid onto the filled bottles to bring the temperature inside the bottles down to a suitable level. This helps prevent the leakage of carbon dioxide gas, ensuring the stability and quality of the products.
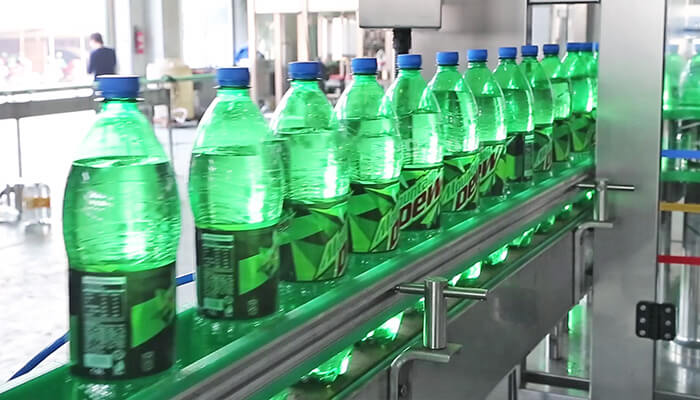
6. Coding and labeling machine
Print the production date, batch number and other information on the bottle to ensure the traceability of each bottle of product.
According to customer requirements and market demand, we provide better solutions for the final product packaging design, such as PVC sleeve labels, BOPP hot glue labels, self-adhesive labels, cold glue paper labels.
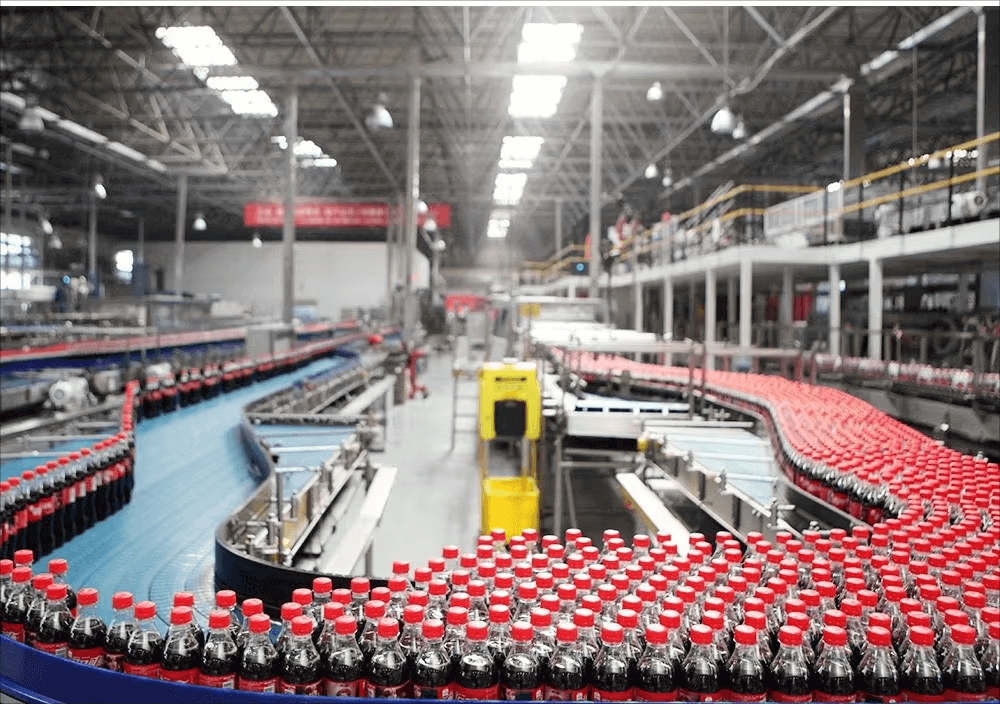
7.Film wrapping machine
The film wrapping machine is used to wrap the labeled bottles in film, ensuring the safety and hygiene of the products during transportation and storage. It protects the bottles from external contamination and helps maintain the products’ condition during long-distance shipping.
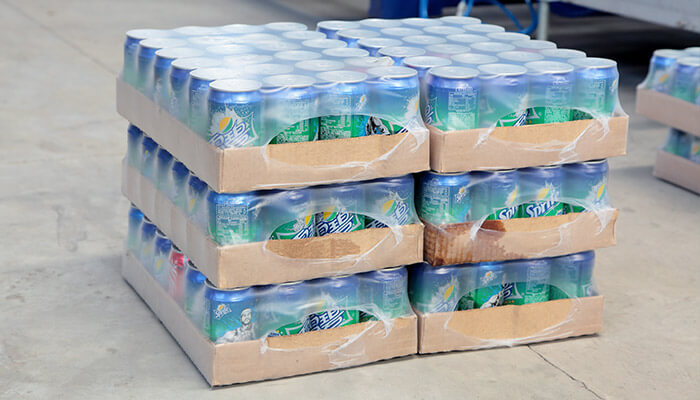
8. Robotic palletizer
The robotic palletizer automatically stacks the packaged bottles onto pallets in a predetermined pattern. This fully automated process streamlines the packaging procedure, ensuring efficient preparation for final shipment and reducing the need for manual labor.